Kaizen was first used alongside the Kanban method in the 1940s and 50s by Toyota to improve the Toyota production system. It’s a framework that promotes continuous improvement. If you’ve asked, “What is Kaizen?” and want to know if leaders can use the best project management software to track continuous improvements, read on. This guide answers these questions and more.
Below, we’ll explain Kaizen and show how it can help organizations increase safety, productivity and employee morale while cutting costs and reducing waste. We’ll cover the seven steps of Kaizen and the framework’s 10 principles, and we’ll list the advantages and disadvantages of this “change for the better” method that can be used with project management methodologies.
Meaning: What Is Kaizen?
Kaizen is a Japanese term that translates to “good change” or “change for the better.” In project management, it has taken on the meaning of continuous improvement, which is a principle of many Agile methodologies like Kanban and Scrum. In a nutshell, Kaizen helps promote a work culture that embraces small incremental changes that create a big impact over time.
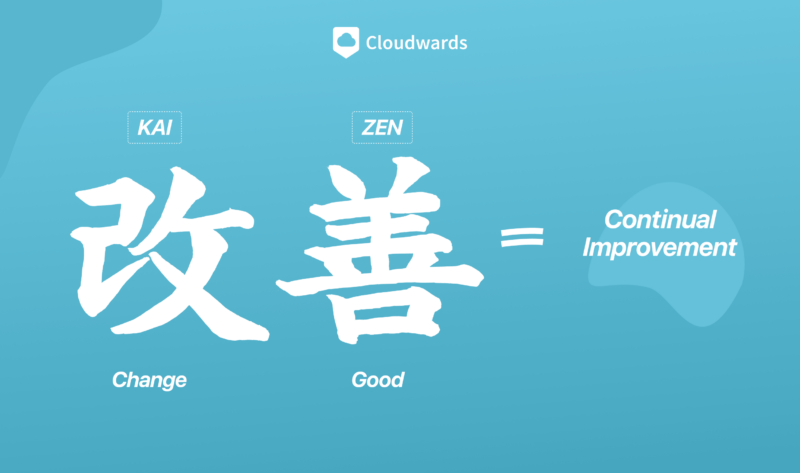
The Kaizen Method and How Kaizen Works
The foundational belief of Kaizen is that everything can be improved and that the status quo or current situation can always be enhanced. Kaizen helps teams focus on identifying issues, creating solutions and implementing them. The Kaizen process never stops, and the idea is to continually improve every aspect of an organization.
Like most methods, Kaizen features a series of steps that can help teams implement the continuous improvement framework. Below, we’ll briefly examine the seven steps of the kaizen cycle and the role they play. The seven steps are as follows:
- Involve employees: The Kaizen concept promotes inclusivity and should involve every team member. Let everyone know you want their feedback to help solve issues and improve processes.
- List your problems: Project managers must listen to their employees and list all the problems presented via feedback. You can then pick an issue to tackle.
- Encourage collaboration and choose a solution: Once you select an issue to fix, encourage your team to work together to find a solution and then collectively decide which solution to use.
- Test the solution: After the team has chosen a solution to the problem, they must test it to see if it fixes or worsens the issue. This event can take between three and five days.
- Analyze the results: Company executives and leaders should analyze the data to determine whether the chosen solution has solved the problem.
- Adopt the solution if successful: If the solution that the team chose has proven successful, it should be adopted and used going forward.
- Repeat the steps often: When one problem has been solved, it’s time to start the process again so that continuous improvements become the norm.
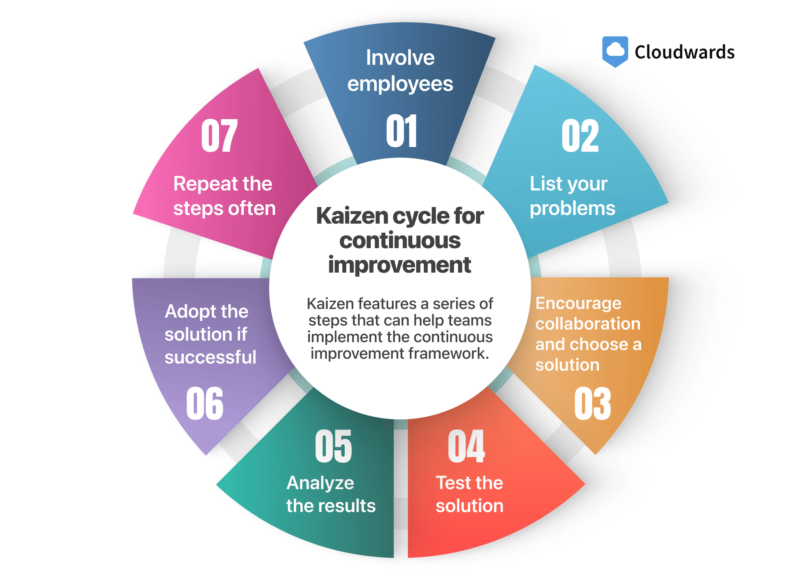
to get the improvement process on track.
What Is a Kaizen Event?
A kaizen event, also known as a kaizen blitz, is a short-term event used to create solutions or brainstorm ideas for solving a problem. Below, we’ll briefly examine the five different types of kaizen events so that you can understand them better.
Types of Kaizen Events
These are the five types of kaizen events that are used to brainstorm solutions to problems in specific departments:
- Point kaizen: As the most widely used kaizen event, point kaizen is a quick improvement event that encourages teams to create a solution to a problem as soon as it is identified. Point kaizen involves little planning and is generally a spur-of-the-moment event.
- System kaizen: System kaizen events feature more planning and organization than point kaizen events, lasting three to five days. They are used to create solutions for system-level and process problems.
- Line kaizen: Line kaizen events solve problems in upstream and downstream departments, forming a line between them. For example, a line event can attempt to solve a problem in the accounting department, which can directly impact the procurement department upstream. These events last three to five days.
- Plane kaizen: Also known as value streams, plane kaizen events are a step above line events as they connect several departments. Short-term plane kaizen events mainly focus on product lines (value streams). Any changes made in one product line department are rolled out to all departments for consistency.
- Cube kaizen: This event connects all planes of an organization via process improvement. The idea is to create and update processes to help an entire organization become lean. This short-term event focuses on improving efficiency, cutting costs and eliminating waste.
10 Principles of the Kaizen Process
The seven Kaizen steps we covered above are built upon 10 guiding principles. The Kaizen principles aren’t complex, but large teams should consider hiring a change manager to make it easier to adopt Kaizen into your workplace. Below, we’ll examine these 10 principles and explain what they mean.
- Embrace new ideas: Kaizen encourages leaders to abandon old processes and problem-solving methods, and it champions the adoption of new processes to solve problems.
- Practice proactive problem-solving: Kaizen encourages teams to raise concerns about potential issues and create solutions before they spiral out of control.
- Don’t accept “no” as an answer: The central belief of Kaizen is that everything can be fixed. If you run into a problem and are told that you can’t overcome an obstacle, don’t accept it. There’s always a solution to be found.
- Don’t let perfection be the enemy of good: We often try to make everything perfect from the start, which can create problems. By adopting the approach of making good, small changes over time, perfection can be reached. Remember the saying, “Rome wasn’t built in a day, but they were laying bricks every hour.” This is the philosophy that Kaizen follows.
- Correct mistakes immediately: Mistakes happen, and they’re okay; we learn from them. What’s not okay is noticing a problem or mistake and not correcting it immediately. Be accountable, accept the problem or own up to the error and find a solution to fix it.
- Empower team members: Kaizen champions empowerment. Getting all employees involved can help increase employee happiness, buy-in and comradery, leading to fresh takes and approaches to problems that may not have been discovered otherwise.
- Ask “why” five times: A key principle of Kaizen is to ask the question “why” five times when faced with a problem. Repeatedly asking “why” can help teams identify the root cause of issues by discovering the problem’s underlying components.
- Listen to multiple people: One person’s knowledge will never transcend the knowledge of many. Gather feedback from as many people as possible. Everyone’s unique take on a problem will lead to unbiased solutions.
- Use data: Hard data can help organizations develop solutions to problems that aren’t just based on personal experience and opinions.
- Improve every day: Kaizen is a continuous process that has no final destination. As soon as one kaizen cycle has been completed, another one starts. The continuous improvement cycle can help organizations and teams become more efficient. You can track improvements via reports in software like monday.com. To learn more, read our monday.com review.
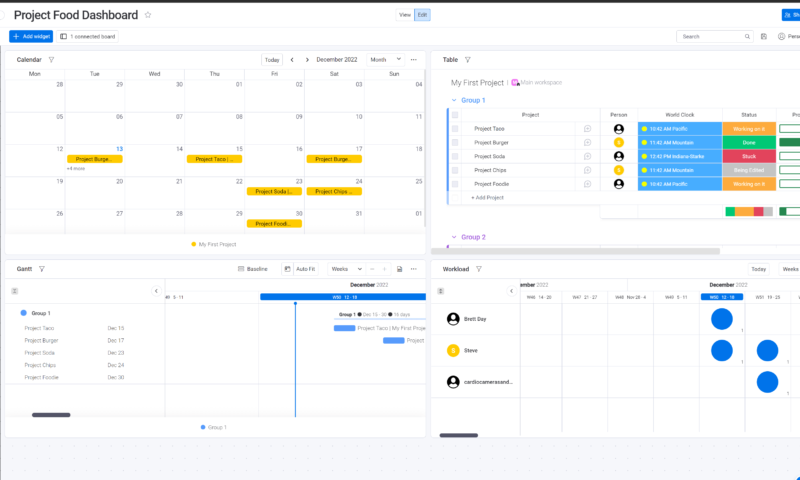
help you analyze data from new initiatives and processes.
What Is Kaizen 5S?
The Kaizen 5S framework is a critical component of the Kaizen method as it helps organizations establish safe, efficient and profitable workspaces. When setting Kaizen efforts into motion, don’t overlook Kaizen 5S. The key components of 5S include the following concepts:
- Seiri (Sort): The process of removing unnecessary items from the workplace.
- Seiton (Set in Order): The process of arranging items logically to speed up workflows.
- Seiso (Shine): The process of keeping your work environment clean.
- Seiketsu (Standardize): The creation of a standardized company-wide cleaning practice.
- Shitsuke (Self-Discipline): Once all is in order, this concept asks for discipline to keep cleaning and safety efforts in place.
The Dual Nature of Kaizen in Business
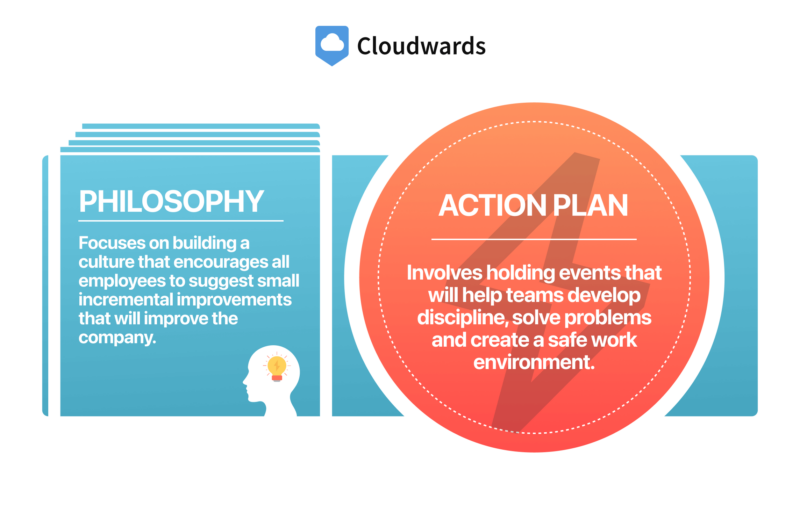
Like the Agile Manifesto, Kaizen is half philosophy and half action plan. When you buy into the philosophy and adopt a Kaizen mindset, implementing improvements — no matter how small or incremental — that can create long-term value becomes easier. Below, we’ll take a quick look at the key elements of the Kaizen action plan and philosophy.
Kaizen Action Plan
- Kaizen events: As discussed above, a key action area of Kaizen is implementing events that help teams solve problems in various business areas.
- Kaizen 5S: The 5S framework helps teams create safe, efficient and profitable workspaces by promoting order, cleanliness and discipline.
Kaizen Philosophy
- Building culture: As a philosophy, Kaizen focuses on building a work culture that encourages every employee in the organization’s structure to suggest and implement small incremental improvements in various departments.
- Lean operations: Kaizen’s philosophy helps organizations become lean by educating everyone about the impact of incremental improvements, by promoting value stream mapping and by identifying waste.
Kaizen Philosophy: Advantages and Disadvantages
As you can imagine, Kaizen has many benefits when implemented properly. However, it also has disadvantages. We’ll look at the pros and cons of Kaizen below.
Kaizen Advantages
Kaizen can help you achieve these goals:
- Enhance manufacturing processes
- Incorporate lean manufacturing
- Eliminate waste
- Improve employee morale
- Increase customer value
- Improve the company’s supply chain
- Find practical solutions to problems
- Increase workplace safety
Kaizen Disadvantages
With Kaizen in place, companies can encounter the following:
- Training challenges
- Resistance to change
- Workplace friction due to differing opinions
- Waning enthusiasm after the Kaizen honeymoon period
Kaizen Project Examples
Many companies have adopted the Kaizen philosophy and its action plans. Below are a few examples of companies that have improved their fortunes by adopting Kaizen.
- Ford Motor Company: In the mid-2000s, Ford was facing bankruptcy. When Alan Mulally — a believer in Lean principles — became the CEO, he implemented Kaizen and made many changes to the company’s culture. This helped bring Ford back from the pit of despair.
- Nestle: Nestle adopted Kaizen and lean manufacturing principles. By soliciting its employees, Nestle has discovered solutions to reduce waste, use its space and resources better, and bring its technology to its full potential.
- Sony: Sony embraced Kaizen when its founder, Akio Morita, discovered the importance of continuous improvement. Morita encouraged Sony’s employees to measure and improve processes rather than just inspect products coming off the production line. In the 1960s, Sony invented the Trinitron TV after its entire workforce cooperated to create new production processes that increased image quality and reduced costs.
Final Thoughts
When Kaizen is used alongside project management methodologies and frameworks, companies can expect to see many workplace improvements. These advancements can include improved profits, waste reduction, higher customer satisfaction and increased worker morale thanks to a friendlier and more inclusive work culture.
It can take a while to feel the effects of Kaizen, and implementing the system can result in some less-than-ideal behaviors. Still, for the most part, those who have adopted the method have created companies that are safer, friendlier, more efficient and more profitable.
Have you implemented the Kaizen method into your business? How was it received? Do your employees feel more valued, and have your business processes improved? Let us know in the comments. Thanks for reading.
FAQ: Kaizen Methodology
-
Kaizen is a framework that helps organizations adopt and implement a culture of continuous improvement.
-
The principles of Kaizen include embracing new ideas, practicing proactive problem-solving, refusing to accept “no” as an answer, not letting perfection be the enemy of good, correcting mistakes immediately, empowering team members, asking “why” five times, listening to multiple people, using data and improving every day.
-
The seven steps of Kaizen are as follows: involve employees, list your problems, encourage collaboration, choose a solution, test the solution, analyze the results, adopt the solution (if successful) and repeat the steps often.
-
Kaizen is a framework that helps improve the workplace by implementing frequent, small changes that can lead to significant improvements over a long period of time.
{“@context”:”https:\/\/schema.org”,”@type”:”FAQPage”,”mainEntity”:[{“@type”:”Question”,”name”:”What Is Kaizen in Simple Words?”,”acceptedAnswer”:{“@type”:”Answer”,”text”:”
Kaizen is a framework that helps organizations adopt and implement a culture of continuous improvement.\n”}},{“@type”:”Question”,”name”:”What Are the Principles of Kaizen?”,”acceptedAnswer”:{“@type”:”Answer”,”text”:”
The principles of Kaizen include embracing new ideas, practicing proactive problem-solving, refusing to accept \u201cno\u201d as an answer, not letting perfection be the enemy of good, correcting mistakes immediately, empowering team members, asking \u201cwhy\u201d five times, listening to multiple people, using data and improving every day.\n”}},{“@type”:”Question”,”name”:”What Are the 7 Steps of Kaizen?”,”acceptedAnswer”:{“@type”:”Answer”,”text”:”
The seven steps of Kaizen are as follows: involve employees, list your problems, encourage collaboration, choose a solution, test the solution, analyze the results, adopt the solution (if successful) and repeat the steps often.\n”}},{“@type”:”Question”,”name”:”What Is Kaizen in the Workplace?”,”acceptedAnswer”:{“@type”:”Answer”,”text”:”
Kaizen is a framework that helps improve the workplace by implementing frequent, small changes that can lead to significant improvements over a long period of time.\n”}}]}
The post What Is Kaizen in Project Management? Definition, Principles and Examples in 2024 appeared first on Cloudwards.